Reliability Engineering Services
"Success is neither magical nor mysterious. Success is the natural consequence of consistently applying basic fundamentals."
Jim Rohn
This is especially true when establishing and maintaining a strong Reliability Based Maintenance Program. Whether you operate with primarily Scheduled maintenance or mostly Condition-based Maintenance (CbM) or perhaps Predicitive Maintenance (PdM) or something in between, it is best to master the fundamentals before pursuing exotic solutions. We have seen many operators and programs really struggle with this and others that have really flourished when conquering the fundamentals first. We understand many of the pitfalls well and can help you avoid them and work with you to point your program in the right direction.
Fleet Reliability Modelling
With Fleet Reliability Modelling, we want to understand and mathematically model your current fleet of engines, aircraft, or other aviation systems that you wish to evaluate as they are operating and performing today.
The first step in the modeling is to perform statistical / Weibull analysis on all of the components within your fleet / system to understand each one’s inherent reliability as well as what type of failure mode each one exhibits (such as wear-out or random or infant mortality). We achieve this using “failure” data (unscheduled events) and “age” data from your maintenance records to most accurately model your fleet and all the conditions it presently operates under.
The second step is to validate all of the Weibull analysis results by creating a computer model / Reliability Block Diagram (RBD). The RBD model simulates scheduled and unscheduled maintenance events and theses simulated results are then compared to your recent historical results. If there are variations, adjustments are made as needed until they most accurately align.
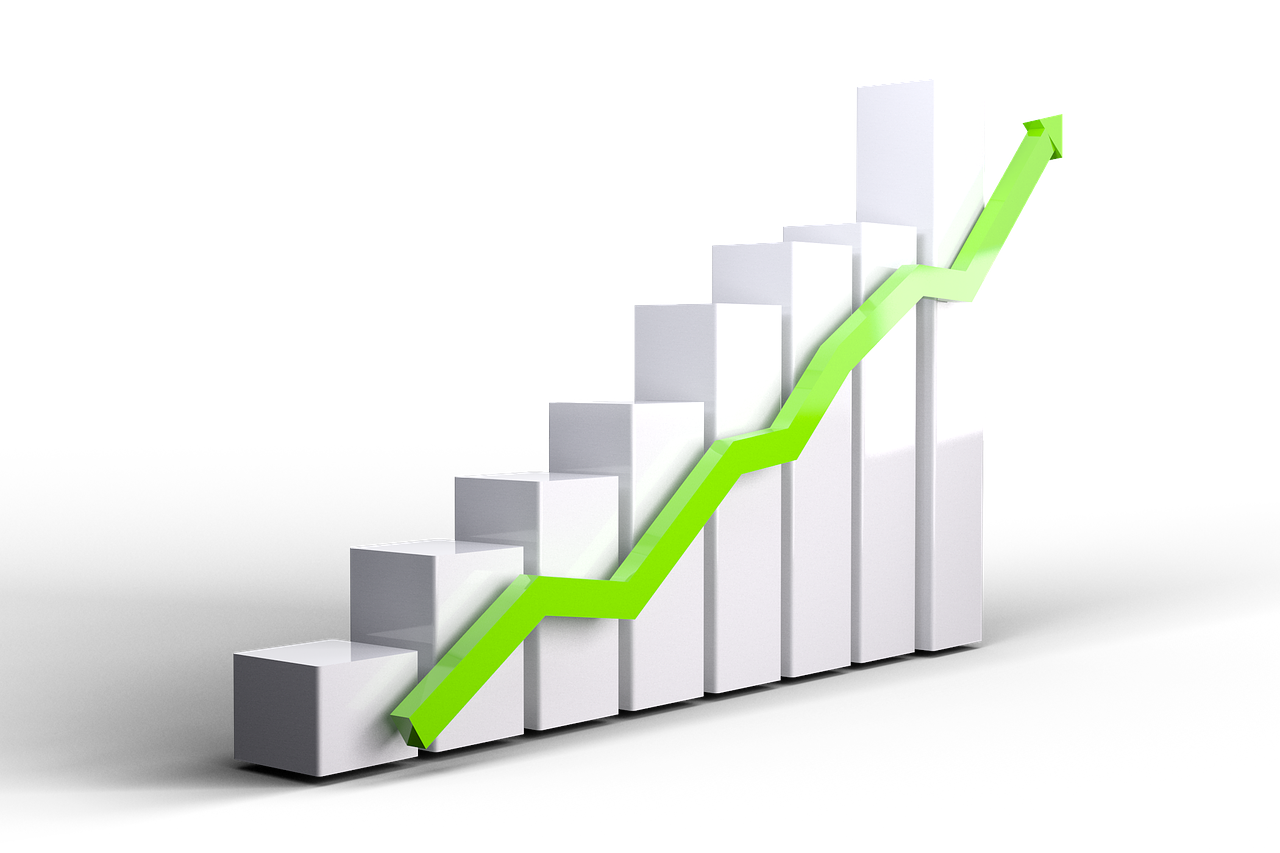
This validated Fleet Reliability Model can now be used to create customized Fleet Maintenance Software for your repair shop(s) with any rules or constraints you wish or need to incorporate.
Note: “age” = how old is an asset or component at the time it experiences an unscheduled event. Specifically, how much calendar time had passed or how many operating hours and cycles had it accrued since brand new (or since being restored to new when applicable).
Fleet Maintenance Software
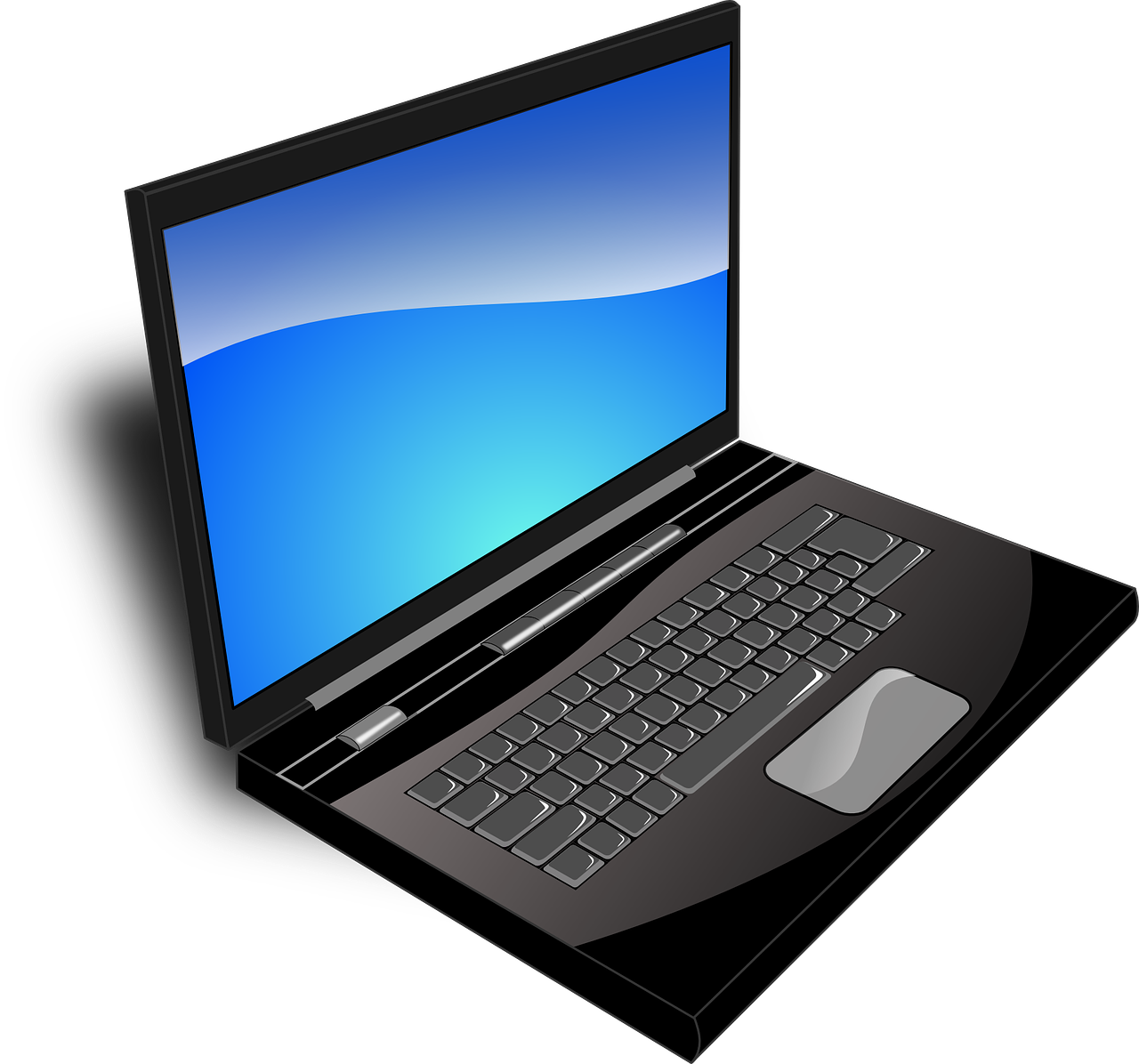
Fleet Maintenance Software combines the Fleet Reliability Model results (all of the components reliability data) plus costs into one software application. The primary function of this software is to evaluate all possible workscopes for an asset in your repair shop, and then to provide your staff with the Optimal Workscope result. The optimal workscope is defined as the workscope that has the highest possible reliability at the lowest possible operating cost. Some operators choose to have higher reliability, understanding it comes with higher operating costs. This and other constraints or rules can be programmed in as desired. Cost data can also be displayed or hidden for different users.
The software can evaluate all possible workscopes automatically as discussed, and it can also be run manually if you want to look at different possible workscopes individually or should you have material constraints that limit you from performing the optimal workscope.
The Fleet Maintenance Software is a great tool to have in that it lets you statistically quantify how long any given workscope will last (on average) as well as the associated total costs and average cost per operating hour. Example: If you perform workscope X on this asset, it will last 3,000 hours (on average) at a total cost of $300,000, which yields an average operating cost of $100 per operating hour. In other words, $300,000/3,000 hours = $100 per operating hour.
The software is also made to accommodate whatever level of maintenance is possible at your location(s) – Operational, Intermediate, and/or Depot.
Note: The Fleet Maintenance software can be made as a stand alone application or in one of a variety of programming languages should you desire to integrate it on your internal network. The latter may require some or much software certification and we are experienced in handling this as well.
Fly Forward Analysis
This is where the magic happens.
Fly Forward Analysis uses computer simulations to fly your fleet of aircraft, engines, or other assets forward in time with whatever scenarios you wish to explore programmed in. The results of the simulations capture the reliability changes, costs, material requirements, and other metrics year over year for whatever duration desired. These are of course key metrics that need to be simulated as accurately as possible in order to best prepare for all future maintenance material requirements and costs.
Virtually any scenario you wish to analyze can be simulated such as:
- Changing / combining maint. types: Scheduled, CbM, PdM, etc.
- Incorporating new components or parts
- Changing LLP hard times / cycles
- A fleet life extension or a fleet retirement study
- Changing operating conditions - cold, hot, desert, high altitude, etc.
- Paying for increased reliability
- Immediate vs. phased-in implementation for any of the above
There are numerous COTS software applications that can do fly forward simulations well to some degree, but most typically have limitations of one kind or another. We utilize custom-made fly forward software so there is virtually no limitation to any scenario you wish to analyze. After all analysis is complete and you have decided on how you want to perform maintenance going forward, the updated rules are programmed into your Fleet Maintenance Software for your staff’s future use.
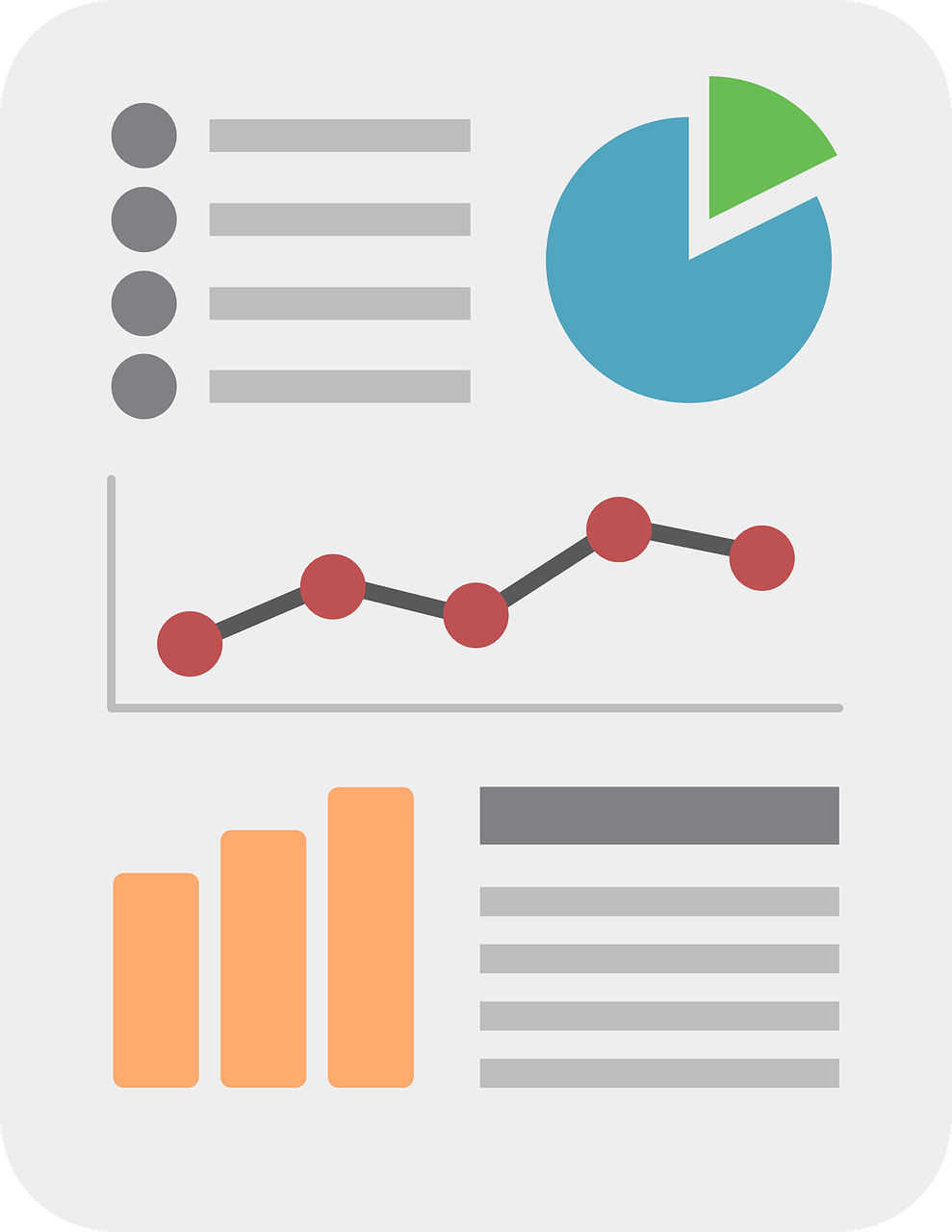
Operators typically choose to simulate current practices first and then numerous other scenarios so they may all be compared and analyzed.
Baseline Study
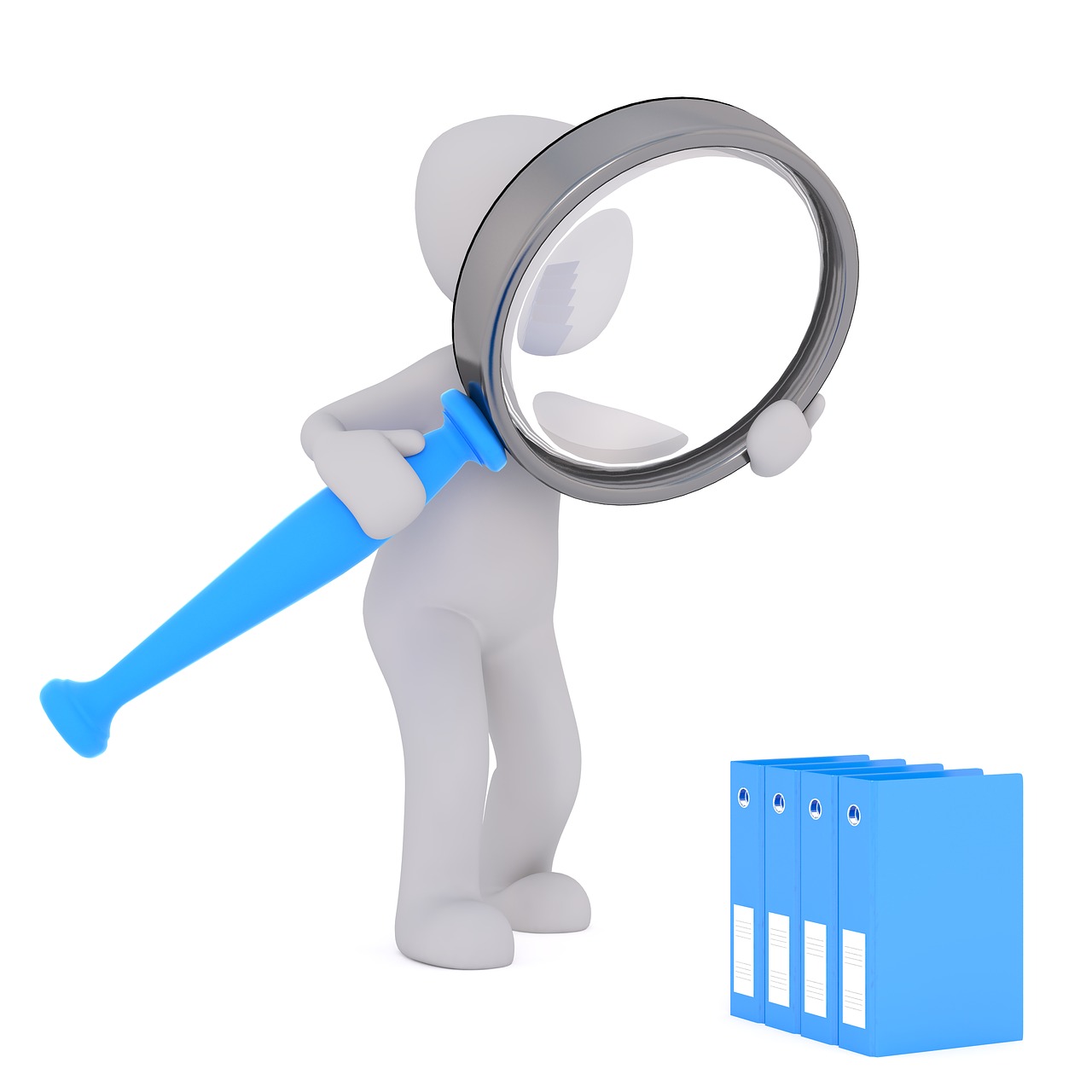
A Baseline Study is typically performed at the start of a new Reliability Based Maintenance Program. This can be for one or several fleets of assets (engines, props, airframes, etc.). The key things we are working to understand are:
- What type of maintenance is in place now - Scheduled, CbP, PdM, etc.?
- What tech data and manuals are used at all maintenance levels?
- What flexibility do you have in changing your maintenance types?
- What maintenance records are captured at all levels - paper & digital?
- How are unscheduled events traced through all maintenance levels?
- What root cause data is being captured for unscheduled events?
- What part / component "age" data is being captured?
- What part / component configuration change data is being captured?
- What maintenance data is generated in-house vs. with contractors?
The objective of the Baseline Study is to understand how much data is in place presently for starting or improving a Reliability Based Maintenance Program. Regardless of where you are with reliability data, we can start with what is in place now and work with you to improve data capturing as appropriate.
Note: We take your privacy and protecting your data very seriously. We will never share your data with other parties or store your data on any 3rd party cloud system (unless you specifically request us to do so for some reason in support of an effort).
Data Collection
Do you need assistance with reliability Data Collection efforts at any of your maintenance / repair sites (Operational, Intermediate, and/or Depot)? If so, we can work to locate veteran maintainers / Subject Matter Experts (SME’s) and contract them to assist you where there is a need.
Utilizing SME’s to assist in reliability programs has worked well with operators in past efforts and has 3 key benefits:
- Captures needed but missing reliability data for future analysis.
- Uses custom made maintenance event tables to record needed data.
- Assistance with troubleshooting unscheduled maintenance events.
OEM’s often have representatives at operator maintenance / repair sites. Data Collection efforts are similar to this with SME’s on site to help you improve your Reliability Based Maintenance Program. The end goal is to to increase your reliability and lower your operating costs within any maintenance constraints you may have or chose to implement.
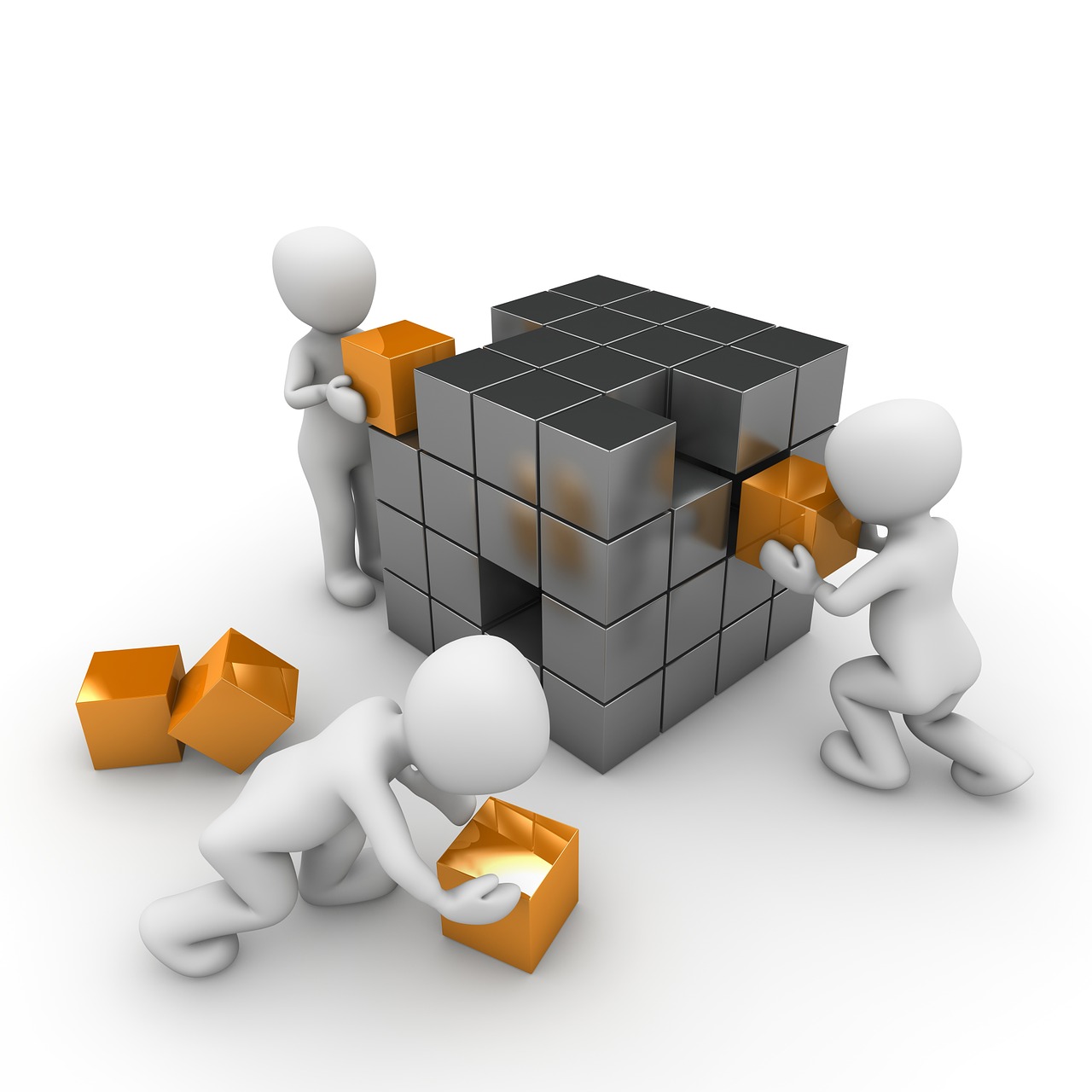
Custom Database
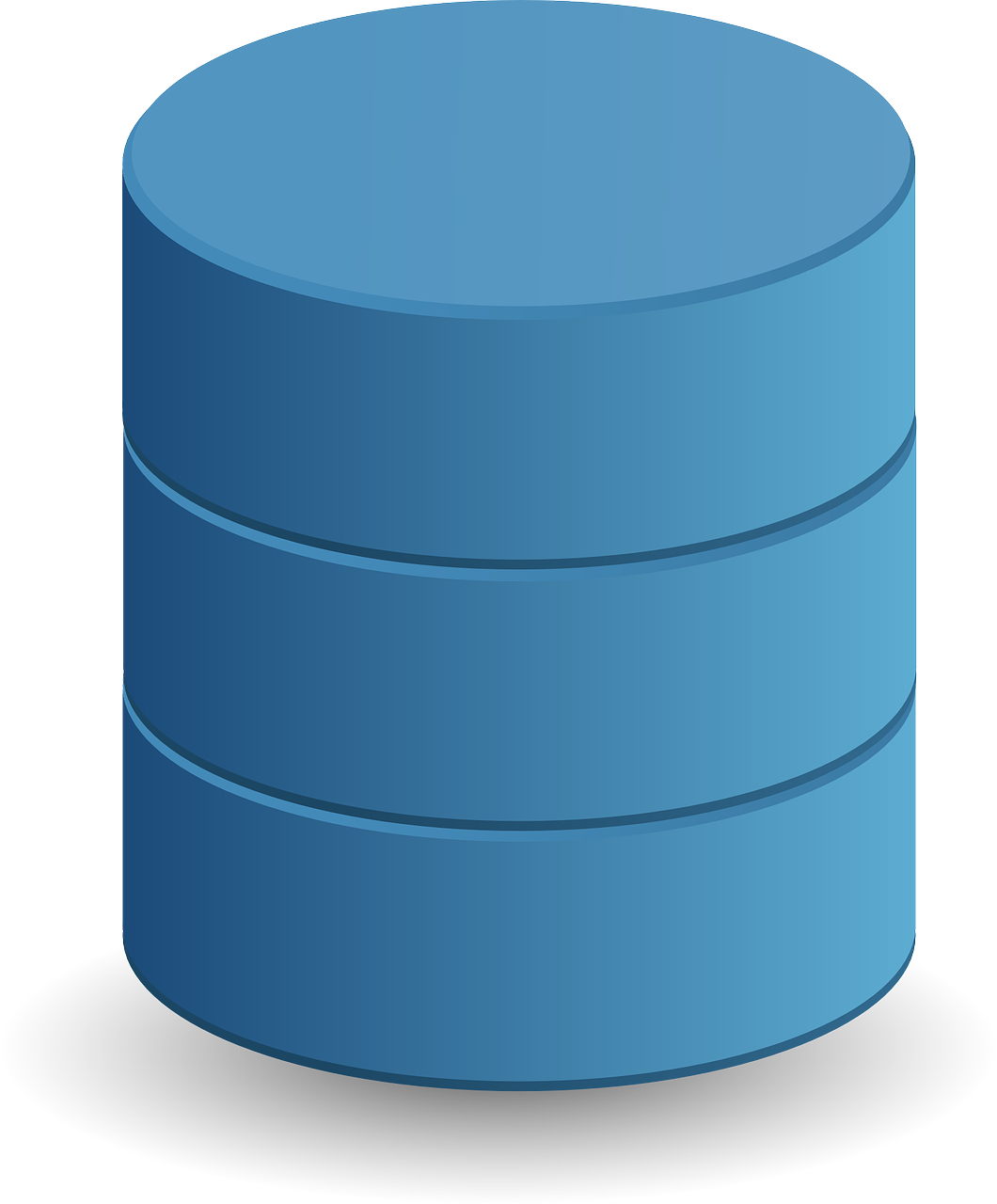
Good Data is central to Reliability Based Maintenance Programs. In order to understand the inherent reliability of any asset within your fleet (without a scheduled hard time), you want certain data captured. Primarily you want to examine all unscheduled events for each of the assets and understand 1) which configuration / design is it (as applicable), 2) what was the “age” [see Note: below] of the asset and its components at the unscheduled event, and finally 3) what was the root cause of the event?
While this sounds relatively straight forward, some of these data elements are sometimes not captured or may be difficult to piece together. This is, understandably, due to numerous maintenance sites, level of capability at each site, and getting appropriate data from maintenance contractors if any involved.
If you have a known need to capture certain reliability data at one of your maintenance / repair sites or if a need is identified during reliability analysis, we can help. We can design a Custom Database for you and your staff to use or work with your IT or other appropriate department to get changes implemented within your database system.
Note: “age” = how old is an asset or component at the time it experiences an unscheduled event. Specifically, how much calendar time had passed or how many operating hours and cycles had it accrued since brand new (or since being restored to new when applicable).